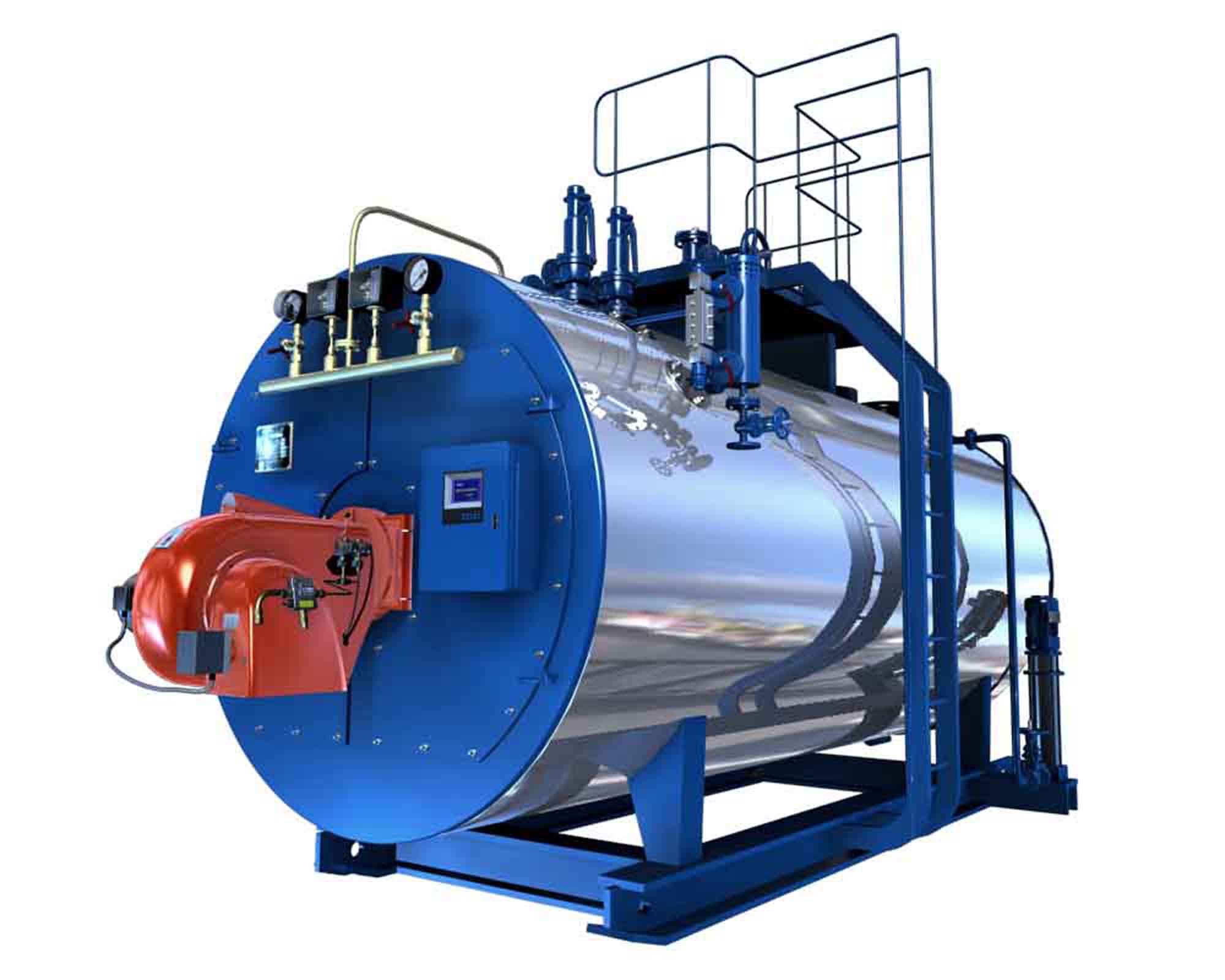
An In-Depth Explanation of Gas Boiler Heating Cycles, Processes, Pressure, and Troubleshooting
Gas boilers are a popular choice for heating homes and buildings due to their efficiency and reliability. Understanding how these boilers work can help homeowners and professionals troubleshoot any issues that may arise.
Gas boilers operate through a heating cycle that involves several key processes. First, the boiler’s burner ignites the gas, creating a flame that heats up the boiler’s heat exchanger. This heat exchanger then transfers the heat to the water or steam that is circulated throughout the system.
During the heating cycle, the boiler’s pump circulates the water or steam through the pipes and radiators, distributing the heat evenly throughout the space. This process continues until the desired temperature is reached, at which point the boiler will either shut off or enter a standby mode to maintain the set temperature.
However, there are certain factors that can affect the efficiency and performance of gas boilers. One important factor is the pressure within the system. Proper pressure is necessary for the boiler to function optimally, and low or high pressure can result in various issues, such as inadequate heating or system failure.
In order to troubleshoot any problems that may arise with a gas boiler, it is important to understand the heating cycles, processes, and pressure involved. By familiarizing themselves with these key aspects of gas boiler operation, homeowners and professionals can effectively diagnose and resolve any issues, ensuring the comfort and functionality of the heating system.
As with any complex system, it is always recommended to consult a licensed professional for any repairs or maintenance on gas boilers. This will ensure that the work is done safely and correctly, minimizing the risk of further damage or safety hazards.
How long is a heating cycle?
The length of a heating cycle in a gas boiler depends on various factors, including the size of the boiler, the desired temperature, and the insulation level of the building. On average, a heating cycle can last anywhere from a few minutes to several hours.
During a heating cycle, the boiler’s burner ignites and heats up the water or air in the system. Once the desired temperature is reached, the burner shuts off, and the heat is distributed throughout the building. As the temperature decreases, the thermostat signals the boiler to start another heating cycle.
In well-insulated buildings with efficient boilers, the heating cycles may be shorter, as the heat is retained for longer periods. On the other hand, in poorly insulated buildings or during extremely cold weather, the heating cycles may be longer to compensate for the heat loss.
It is important to note that the duration of a heating cycle can also be affected by the boiler’s settings and controls. Some boilers have adjustable heating cycles, allowing the user to customize the duration based on their preferences and energy-saving goals.
In general, it is recommended to consult the boiler’s manual or contact a professional technician to determine the optimal duration for a heating cycle in a specific system. This can help ensure proper comfort levels, energy efficiency, and avoid potential issues such as short cycling or overheating.
Regular maintenance and troubleshooting can also help identify any problems that may affect the duration of heating cycles, such as faulty sensors, clogged filters, or inadequate water pressure. By addressing these issues promptly, homeowners can optimize the performance of their gas boilers and ensure consistent and efficient heating throughout the year.
Average frequency of firing
The average frequency of firing refers to how often the gas boiler ignites and burns fuel in order to generate heat. This frequency is dependent on various factors, including the temperature settings, the size of the space being heated, and the insulation of the building.
Gas boilers are designed to be efficient and only fire when necessary to maintain the desired temperature. They are equipped with sensors that monitor the temperature of the water or air being heated, and when the temperature falls below the set point, the boiler will ignite and start the heating cycle.
The frequency of firing can vary greatly depending on the heating demands of the building. In colder climates or during colder months, the boiler may need to fire more frequently to keep up with the demand for heat. Conversely, in milder climates or during warmer months, the boiler may fire less often.
It is important to note that frequent firing can result in increased energy consumption and higher fuel costs. Therefore, it is recommended to set the temperature settings of the boiler appropriately to avoid unnecessary firing and energy waste.
In some cases, a gas boiler may have a modulation feature that allows it to adjust the firing rate based on the heating demand. This can help optimize energy usage and reduce fuel consumption.
If you notice that your gas boiler is firing excessively or not firing enough, it may be a sign of an underlying issue. It is recommended to consult a professional technician to diagnose and resolve any problems with the boiler.
Factors affecting cycle length
The cycle length of a gas boiler refers to the duration of each heating cycle, which includes the time it takes for the boiler to heat up and the time it takes for it to cool down. Several factors can affect the length of the heating cycle, including:
Factor | Description |
---|---|
Thermostat settings | The temperature set on the thermostat can determine how often the boiler turns on and off. Higher thermostat settings may result in shorter heating cycles as the boiler works harder to reach the desired temperature. |
Insulation | The level of insulation in a building can affect how quickly heat is lost, which in turn can impact the cycle length. Well-insulated buildings may have longer heating cycles as they retain heat more efficiently. |
Weather conditions | Cold weather can cause the boiler to work harder to maintain the set temperature, leading to shorter heating cycles. On the other hand, mild weather may result in longer heating cycles as less heat is required. |
Boiler size | The size and capacity of the boiler can influence the cycle length. A larger boiler may have shorter heating cycles as it can produce more heat in a shorter amount of time. |
Piping and distribution system | The efficiency of the piping and distribution system can impact the cycle length. Well-designed systems with minimal heat loss may result in longer heating cycles. |
Boiler maintenance | A well-maintained boiler is more likely to operate efficiently, which can affect the cycle length. Regular maintenance, such as cleaning and inspecting the boiler, can help optimize its performance. |
By considering these factors, homeowners and technicians can better understand and manage the cycle length of a gas boiler, ensuring optimal heating efficiency and comfort.
What are the 4 heating processes?
When it comes to gas boilers, there are four main heating processes that take place: ignition, combustion, heat transfer, and exhaust.
The first process, ignition, involves the start-up of the gas boiler. When the thermostat signals a need for heat, the ignition process begins. This typically involves a spark or a pilot flame igniting the gas fuel, allowing for combustion to occur.
Once ignition has taken place, the combustion process begins. Combustion involves the burning of the gas fuel, which releases heat energy. This process takes place within the combustion chamber of the boiler and is crucial for generating the heat needed for the heating system.
The third process, heat transfer, is where the generated heat is transferred to the water or air that will be used to heat the space. In a gas boiler, this typically involves the heat passing through a heat exchanger, where the water or air absorbs the heat energy. The heated water or air is then circulated through the heating system to provide warmth.
Finally, the exhaust process occurs when the byproducts of combustion, such as carbon dioxide and water vapor, are expelled from the boiler through the flue. This ensures that the combustion process is complete and that the boiler operates safely and efficiently. The exhaust gases are often vented outside the building to prevent any potential health hazards.
Heating Process | Description |
---|---|
Ignition | The start-up of the gas boiler, involving the ignition of the gas fuel. |
Combustion | The burning of the gas fuel, which releases heat energy. |
Heat Transfer | The transfer of the generated heat to the water or air for heating purposes. |
Exhaust | The expulsion of the byproducts of combustion from the boiler. |
Convection
Convection is a vital process in gas boilers that contributes to the overall heating efficiency. It involves the transfer of heat through the movement of fluids, such as air or water, due to differences in temperature.
In a gas boiler, convection occurs when the burner heats the water or air in the system. As the fluid is heated, it becomes less dense and rises, creating a convection current. This upward movement carries the heat to different parts of the system, distributing it evenly and effectively.
Convection plays a crucial role in heating cycles, as it helps to transfer heat from the burner to the water or air that needs to be warmed. Without convection, the heat would stay localized around the burner, resulting in inefficient heating.
Gas boilers are designed to optimize convection by incorporating features such as heat exchangers and pipes to facilitate the movement of fluids. The heat exchanger provides a large surface area for the transfer of heat, while the pipes direct the flow of fluids to ensure efficient convection.
However, issues with convection can occur in gas boilers, leading to reduced heating efficiency. Common problems include blockages in the pipes or heat exchangers, which hinder the movement of fluids and restrict convection. These issues can be resolved through regular maintenance and cleaning of the system.
Overall, convection is a fundamental process in gas boilers that enables efficient heating by transferring heat through the movement of fluids. Understanding how convection works can help in troubleshooting and maintaining the performance of gas boilers.
Radiation
Radiation is one of the three main ways heat is transferred in a gas boiler. It occurs when heat energy is emitted in the form of electromagnetic waves. In a gas boiler, radiation occurs mainly from the hot combustion gases and the surfaces of the boiler.
When the burner in the gas boiler ignites, it produces hot combustion gases that pass through the heat exchanger. As these gases move through the heat exchanger, they emit radiant heat energy. This radiant heat is then absorbed by the surfaces of the heat exchanger, which in turn transfer it to the water or air circulating in the system.
In addition to the radiant heat emitted by the combustion gases, the surfaces of the boiler itself also emit radiation. This occurs when the surfaces of the boiler are hotter than the surrounding environment. The hot surfaces emit radiant heat, which can be absorbed by nearby objects or surfaces.
Radiation is an important heat transfer mechanism in a gas boiler, as it allows for the efficient transfer of heat from the combustion gases to the water or air in the system. By maximizing the surface area of the heat exchanger and optimizing the design of the boiler’s surfaces, gas boilers can effectively utilize radiation to heat the system.
- Radiation is one of the main ways heat is transferred in a gas boiler.
- It occurs when heat energy is emitted in the form of electromagnetic waves.
- Radiation in a gas boiler mainly comes from the hot combustion gases and the surfaces of the boiler.
- The radiant heat emitted by the combustion gases is absorbed by the surfaces of the heat exchanger, which transfer it to the water or air circulating in the system.
- The surfaces of the boiler itself also emit radiation when they are hotter than the surrounding environment.
- By maximizing the surface area of the heat exchanger and optimizing the design of the boiler’s surfaces, gas boilers can effectively utilize radiation to heat the system.
Conduction
In the context of gas boilers, conduction refers to the transfer of heat from one object to another through direct contact. When a gas boiler is operating, it generates heat by burning fuel, such as natural gas or propane. This heat is then transferred to the water or air that is in contact with the boiler’s heat exchanger.
Conduction is an important process in gas boilers because it allows for efficient heat transfer. The heat exchanger, which is typically made of metal, has a high thermal conductivity, meaning it can quickly and effectively transfer heat from the burning fuel to the water or air. This ensures that the heat generated by the boiler is efficiently distributed throughout the heating system.
During the heating cycle, the heat exchanger in a gas boiler becomes hot as the fuel is burned. The hot exchanger then transfers heat to the water or air that passes through it. This heated water or air is then circulated throughout the heating system, providing warmth to the various rooms or spaces.
In troubleshooting gas boilers, conduction plays a role in diagnosing and resolving issues related to heat transfer. If the heat exchanger is not functioning properly or is damaged, it may not transfer heat effectively, leading to reduced heating efficiency or inadequate heating. In such cases, the heat exchanger may need to be repaired or replaced to restore proper conduction and heat transfer.
Overall, conduction is a fundamental process in gas boilers that allows for efficient heat transfer and ensures effective heating of water or air. Understanding how conduction works can help homeowners and technicians diagnose and resolve issues with their gas boiler systems.
Mass transfer
Mass transfer refers to the movement of substances from one place to another. In the context of gas boilers, mass transfer is an important process that occurs during the combustion of fuel. When fuel is burned in a gas boiler, it undergoes a chemical reaction with oxygen to produce heat and various combustion byproducts, such as water vapor and carbon dioxide.
During combustion, mass transfer occurs as the fuel and air mixture inside the boiler is heated. This heat causes the fuel molecules to break apart, releasing energy and creating combustion byproducts. These byproducts then move from the combustion chamber to the flue gas vent, where they are expelled from the boiler.
Mass transfer is also involved in the heating cycle of a gas boiler. As the boiler heats up, heat is transferred from the burner to the water in the boiler’s heat exchanger. This transfer of heat is facilitated by the movement of molecules within the water. The heated water then circulates through the heating system, transferring heat to the surrounding environment.
Understanding mass transfer is important for troubleshooting gas boilers. If there is a problem with mass transfer, it can lead to reduced efficiency and performance issues. For example, if there is insufficient air supply to the combustion chamber, it can result in incomplete combustion and the production of harmful combustion byproducts, such as carbon monoxide.
Mass transfer plays a crucial role in the operation of gas boilers. It is involved in the combustion process and the transfer of heat within the boiler. By understanding mass transfer, homeowners and technicians can better diagnose and address issues with gas boilers.
How does a gas boiler heat water?
A gas boiler is a common heating appliance that uses natural gas or propane to heat water. The heated water is then circulated through a system of pipes and radiators or baseboard heaters to provide warmth in a home or building.
Here is a step-by-step process of how a gas boiler heats water:
- Ignition: When the thermostat signals a need for heat, the gas boiler’s pilot light ignites the burner.
- Combustion: The burner draws in gas and mixes it with air, creating a controlled flame inside the combustion chamber. This flame heats the water.
- Heat exchanger: The heat from the combustion chamber is transferred to the water through a heat exchanger. The heat exchanger is a metal component that allows the transfer of heat without mixing the combustion gases with the water.
- Circulation: The hot water produced by the gas boiler is then circulated through a system of pipes. This system can include radiators, baseboard heaters, or underfloor heating pipes.
- Thermostat control: The thermostat monitors the temperature in the rooms and signals the gas boiler to turn on or off accordingly. This helps maintain a comfortable indoor temperature.
- Condensation (in some models): Some gas boilers are designed to condense the water vapor in the combustion gases, increasing efficiency. This process extracts additional heat from the flue gases and reduces energy waste.
A gas boiler heats water through the combustion of gas, transfers the heat to the water through a heat exchanger, and circulates the hot water to provide heating in a home or building. The thermostat controls the operation of the gas boiler based on the desired indoor temperature.
Principle of operation
A gas boiler works by using natural gas or propane to heat water, which is then circulated throughout the heating system to provide warmth. The boiler consists of a burner, heat exchanger, and controls.
When the thermostat detects that the temperature in the building has dropped below the desired level, it sends a signal to the boiler to start the heating process. The burner ignites the gas, creating a flame that heats up the heat exchanger.
The heat exchanger is a metal component that allows heat to transfer from the burner flame to the water. As the water passes through the heat exchanger, it absorbs the heat, increasing its temperature. The hot water is then pumped out of the boiler and circulated through the radiators or underfloor heating system in the building.
As the hot water flows through the radiators, it releases heat into the surrounding air, warming up the room. The cooled water then returns to the boiler to be reheated and recirculated, creating a continuous heating cycle.
The boiler’s controls monitor the temperature of the water and adjust the burner’s flame accordingly to maintain the desired temperature. If the water temperature exceeds the set level, the burner will turn off until the temperature drops again.
In addition to providing heat, gas boilers also have other safety features. For example, they are equipped with a pressure relief valve that releases excess pressure if it builds up in the system. Gas boilers also have a flue that vents the combustion gases outside, preventing them from accumulating indoors.
If there is a problem with the gas boiler, such as a lack of heat or unusual noises, troubleshooting may be required. Common issues can include a faulty thermostat, a blocked flue, or a malfunctioning pressure relief valve. It is important to consult a professional technician to diagnose and fix any boiler problems.
Role of heat exchanger
The heat exchanger is a crucial component in a gas boiler, as it plays a vital role in the heating process. Its main function is to transfer heat from the burning gas to the water that flows through it. This transfer of heat allows the water to reach the desired temperature for heating the building.
A heat exchanger consists of a series of tubes or pipes that are designed to maximize the surface area available for heat transfer. The burning gas flows through these tubes, while the water circulates around them. As the hot gas passes through the tubes, it gives off heat to the surrounding water, which then absorbs the heat and becomes hot.
The heat exchanger also helps to improve the efficiency of the heating system by recapturing and reusing some of the heat that would otherwise be wasted. By transferring heat from the hot gas to the water, the heat exchanger helps to minimize energy loss and maximize the heating output.
However, over time, the heat exchanger can become dirty or corroded, which can affect its performance. If the heat exchanger is clogged or damaged, it may not transfer heat effectively, resulting in reduced heating efficiency or even a complete breakdown of the boiler. Regular maintenance and cleaning of the heat exchanger are important to ensure its proper functioning and prevent any potential issues.
Advantages | Disadvantages |
---|---|
Efficient heat transfer | Potential for corrosion or clogging |
Energy-saving | Requires regular maintenance |
Maximizes heating output | Possible heat exchanger failure |
The heat exchanger is a critical component in a gas boiler, as it is responsible for transferring heat from the burning gas to the water. It helps to improve the efficiency of the heating system and ensures that the water reaches the desired temperature for heating the building. Regular maintenance and cleaning are necessary to keep the heat exchanger functioning properly and prevent any potential issues.
Water circulation in the system
Water circulation is a crucial process in gas boiler systems, as it allows for the distribution of heat throughout the system and ensures that all areas are adequately heated. The circulation process is driven by a pump that is typically located near the boiler.
When the boiler is turned on, the pump activates and starts circulating the water through the system. The water is heated by the boiler and then transported through pipes to radiators or other heat emitters in various rooms of the building. The heated water transfers its heat to the surrounding air, warming up the room.
The cooled water then returns to the boiler through a separate set of pipes, completing the circulation loop. This return water is typically cooler than the supply water, as it has released its heat to the environment. As the return water enters the boiler, it is reheated and the cycle continues.
It is important to ensure proper water circulation in the system to maintain efficient heating. If there are any issues with circulation, it can result in uneven heating or even complete failure of the system. Common problems that can affect water circulation include pump failure, blockages in the pipes, or airlocks in the system.
Regular maintenance and inspection of the system can help identify and resolve any circulation issues. This may involve checking the pump for proper operation, flushing the system to remove any debris or blockages, and bleeding any air trapped in the pipes.
Water circulation is a vital process in gas boiler systems, allowing for the efficient distribution of heat throughout the building. Understanding how water circulates in the system and addressing any circulation issues promptly can help ensure optimal performance and comfort.
What is the normal boiler pressure?
The normal boiler pressure refers to the pressure at which the boiler operates during its normal functioning. It is an important parameter that needs to be maintained within a certain range for the boiler to function properly and efficiently.
For most gas boilers, the normal operating pressure is typically around 1-1.5 bar. However, the exact pressure may vary depending on the specific make and model of the boiler. It is important to consult the manufacturer’s instructions or a qualified heating engineer to determine the appropriate pressure range for your particular boiler.
If the boiler pressure is too low, it can lead to inadequate heating and hot water supply. On the other hand, if the pressure is too high, it can put unnecessary strain on the boiler and its components, potentially leading to leaks or other malfunctions.
To ensure that the boiler pressure remains within the normal range, it is recommended to regularly check the pressure gauge on the boiler. If the pressure is too low, it can be increased by adding water to the system. Conversely, if the pressure is too high, it can be reduced by bleeding some water from the radiators or using the pressure relief valve.
If you are unsure about the normal pressure range for your boiler or if you notice any abnormal fluctuations in the pressure, it is advisable to contact a qualified heating engineer who can assess the situation and make any necessary adjustments or repairs.
Recommended pressure
The recommended pressure for a gas boiler is typically between 1.0 and 1.5 bar. This range ensures that the system is operating efficiently and safely. If the pressure is too low, it can lead to a loss of heat and inadequate hot water production. On the other hand, if the pressure is too high, it can cause damage to the boiler and its components.
To check the pressure of your gas boiler, you can use the pressure gauge on the front of the unit. If the pressure is below the recommended range, you can increase it by adding water to the system. This can be done by opening the filling loop valve and allowing water to enter the system until the pressure reaches the desired level. However, it is important to be cautious and not overfill the system, as this can also cause problems.
If you are unsure about the recommended pressure for your specific boiler model, it is best to consult the manufacturer’s instructions or contact a professional heating engineer for assistance. They can provide guidance on maintaining the correct pressure and ensure that your boiler is operating safely and efficiently.
Causes of increased/decreased pressure
Gas boilers operate within a specific pressure range to ensure optimal performance and safety. However, there are several factors that can cause pressure to increase or decrease beyond the recommended levels. Understanding these causes can help in troubleshooting and resolving pressure-related issues.
Causes of increased pressure:
- Overheating: If the boiler is operating at high temperatures, it can lead to increased pressure. This can be caused by a faulty thermostat or a malfunctioning pressure relief valve.
- Blockage in the system: Accumulation of debris, sludge, or scale in the pipes or heat exchanger can restrict the flow of water, causing pressure to build up.
- Expansion vessel issues: The expansion vessel is responsible for absorbing the expansion of water as it heats up. If the vessel is faulty or incorrectly sized, it can result in increased pressure.
- Water supply pressure: If the incoming water supply has high pressure, it can cause the boiler pressure to rise. This can be resolved by installing a pressure reducing valve.
Causes of decreased pressure:
- Leakage in the system: A leak in the boiler or the central heating system can lead to a loss of pressure. Common areas where leaks occur include valves, fittings, and pipes.
- Bleeding of radiators: When air enters the heating system, it can cause a decrease in pressure. Regularly bleeding the radiators can help remove trapped air and maintain proper pressure.
- Loss of water: If there is a loss of water in the system, either due to a leak or evaporation, it can result in decreased pressure. Checking for leaks and topping up the water level can help resolve this issue.
- Faulty pressure relief valve: If the pressure relief valve is not functioning correctly, it may release excessive water, leading to a decrease in pressure.
It is important to regularly monitor the pressure of your gas boiler and address any issues promptly to ensure its safe and efficient operation.
How to adjust pressure
Adjusting the pressure on a gas boiler is an important maintenance task that should be carried out regularly to ensure the smooth operation of the boiler. The pressure in a gas boiler is typically measured in units of bar, with the recommended pressure range usually stated in the boiler’s instruction manual.
To adjust the pressure, you will need to locate the pressure gauge on your boiler. This is usually located on the front panel of the boiler and is marked with a scale ranging from low to high pressure. The pressure gauge will have a needle that indicates the current pressure level.
Before adjusting the pressure, it is important to turn off the boiler and allow it to cool down. Once the boiler has cooled down, you can begin adjusting the pressure by following these steps:
- Locate the filling loop valve, which is usually located near the boiler.
- Ensure that the filling loop valve is securely connected to the water supply.
- Slowly open the filling loop valve by turning it in a clockwise direction.
- Observe the pressure gauge and wait for the needle to reach the desired pressure level.
- Once the desired pressure level is reached, close the filling loop valve by turning it in a counterclockwise direction.
- Check the pressure gauge again to ensure that the pressure remains within the recommended range.
- If the pressure is too high or too low, repeat the above steps until the correct pressure is achieved.
It is important to note that adjusting the pressure on a gas boiler should only be done by a qualified professional. If you are unsure about how to adjust the pressure or if you experience any issues with your gas boiler, it is recommended to contact a licensed heating engineer for assistance.
By regularly adjusting the pressure on your gas boiler, you can ensure optimal performance and prolong the lifespan of your boiler.
Pros | Cons |
---|---|
Improves boiler efficiency | Requires professional expertise |
Prevents boiler damage | Incorrect adjustments can cause system failure |
Prolongs boiler lifespan | May require additional tools or equipment |
How do I reset my boiler?
If you are experiencing issues with your gas boiler, resetting it may help to resolve the problem. Here are the steps to reset your boiler:
- Turn off the boiler: Locate the power switch or control panel for your boiler and turn it off. This will shut down the boiler and allow it to reset.
- Wait for a few minutes: Give your boiler some time to completely power down. This will allow any sensors or components to reset.
- Turn the boiler back on: After waiting for a few minutes, turn the power switch or control panel back on to restart the boiler.
- Monitor the boiler: Once the boiler is back on, pay attention to any error codes or warning lights that may appear. This information can help diagnose the problem.
- Contact a professional: If resetting the boiler does not resolve the issue or if you are unsure about the problem, it is recommended to contact a qualified technician or plumber. They will be able to assess the situation and provide the necessary repairs or maintenance.
Note: It is important to follow the manufacturer’s instructions when resetting your boiler, as the process may vary depending on the make and model.
Resetting your boiler is a simple troubleshooting step that can often resolve minor issues. However, if you are not comfortable performing the reset or if the problem persists, it is always best to seek professional help to avoid any further damage or safety hazards.
Determining if reboot is needed
In some cases, troubleshooting gas boilers may require a reboot of the system. Rebooting the boiler can often resolve minor issues and restore normal functioning.
Here are some signs that indicate a reboot may be needed:
- The boiler is not responding to commands or controls.
- There is no heat or hot water coming from the boiler.
- The boiler is displaying error codes or error messages.
- Unusual noises are coming from the boiler.
- The boiler is constantly cycling on and off.
If you notice any of these signs, it is recommended to try rebooting the boiler before calling a professional for assistance. Rebooting the system can often resolve temporary glitches or software issues that may be causing the problem.
To reboot the boiler, follow these steps:
- Locate the power switch or circuit breaker that controls the boiler.
- Turn off the power to the boiler by flipping the switch or tripping the circuit breaker.
- Wait for approximately 30 seconds to 1 minute.
- Turn the power back on by flipping the switch or resetting the circuit breaker.
- Wait for the boiler to restart and go through its startup sequence.
After the reboot, monitor the boiler to see if the issue has been resolved. If the problem persists, it is recommended to contact a qualified technician to diagnose and repair the boiler.
Reboot instructions for user
If you are experiencing issues with your gas boiler, a simple reboot may help resolve the problem. Follow these instructions to safely and effectively reboot your boiler:
- Locate the power switch for your boiler. This is typically found near the boiler itself or on the control panel.
- Switch the power off by flipping the power switch to the “off” position. Wait for at least 30 seconds before proceeding to the next step.
- After the waiting period, turn the power back on by flipping the power switch to the “on” position.
- Observe the boiler to ensure that it is restarting properly. You may hear the boiler firing up or see lights indicating that it is operational.
- Wait for the boiler to complete its startup cycle. This typically takes a few minutes. During this time, avoid adjusting any settings or turning off the power again.
- If the boiler does not start up or if the issue persists, it is recommended to contact a qualified technician for further assistance.
Remember to exercise caution when rebooting your gas boiler. If you are unsure or uncomfortable with the process, it is best to seek professional help to avoid any potential hazards.
When to call an engineer
Gas boilers are complex systems that require regular maintenance and occasional repairs to ensure they are operating safely and efficiently. While some boiler issues can be resolved without professional help, there are certain situations where it is best to call an engineer. Here are some signs that indicate you should contact a qualified professional:
1. No heating or hot water | If your boiler is not providing any heat or hot water, it could indicate a serious problem with the system. An engineer will be able to diagnose the issue and determine the necessary repairs. |
2. Strange noises or smells | If you notice any unusual noises, such as banging, whistling, or gurgling, coming from your boiler, it could be a sign of a mechanical problem. Similarly, if you detect any strange smells, like gas or burning, it is important to contact an engineer immediately. |
3. Leaks or drips | If you notice any water leaks or drips around your boiler, it could indicate a faulty component or a problem with the system’s pressure. A qualified engineer will be able to identify the source of the leak and fix it accordingly. |
4. Low pressure | If the pressure gauge on your boiler indicates low pressure, it could mean that there is a problem with the water supply or a leak in the system. An engineer will be able to assess the situation and determine the appropriate course of action. |
5. High pressure | Conversely, if the pressure gauge shows high pressure, it could indicate an issue with the pressure relief valve or another component of the system. It is important to have an engineer inspect the boiler to prevent any potential damage or safety hazards. |
6. Pilot light issues | If the pilot light on your boiler keeps going out or is a different color than usual, it could be a sign of a ventilation problem or a faulty thermocouple. An engineer will be able to diagnose the issue and make the necessary repairs or replacements. |
Remember, it is always better to be safe than sorry when it comes to boiler issues. If you are unsure about any aspect of your boiler’s performance, it is best to call a qualified engineer who can provide expert advice and assistance.
Why does my boiler keep cutting out?
There are several reasons why your boiler may keep cutting out. Some of the most common reasons include:
1. Low water pressure: If the water pressure in your boiler is too low, it may cause the boiler to cut out. This can be due to a leak in the system or a problem with the pressure relief valve. |
2. Faulty thermostat: If the thermostat on your boiler is faulty, it may not be able to accurately measure the temperature of the water. This can cause the boiler to cut out as a safety precaution. |
3. Blocked condensate pipe: If the condensate pipe, which carries waste water away from the boiler, becomes blocked, it can cause the boiler to cut out. This is a common problem during cold weather when the pipe can freeze. |
4. Faulty pump: If the pump in your boiler is not working properly, it may not be able to circulate the water effectively. This can cause the boiler to cut out as a safety precaution. |
5. Air in the system: If there is air trapped in the system, it can prevent the water from circulating properly. This can cause the boiler to cut out and may also lead to cold spots in your radiators. |
If your boiler keeps cutting out, it is recommended to contact a qualified heating engineer to diagnose and fix the problem. Attempting to fix the issue yourself may be dangerous and could void any warranties on your boiler.
Possible causes of shutdown
Gas boilers can shut down for various reasons. Here are some possible causes:
- Ignition failure: If the gas boiler fails to ignite, it will automatically shut down as a safety precaution. This can be caused by a faulty ignition system or a lack of gas supply.
- Overheating: If the boiler’s temperature exceeds the safe limit, it will shut down to prevent damage. Overheating can be caused by a malfunctioning thermostat or a blocked heat exchanger.
- Low water pressure: When the boiler’s water pressure drops below the recommended level, it can shut down to avoid further damage. Low water pressure can be caused by a leak in the system or a faulty pressure relief valve.
- Faulty sensors: Gas boilers have various sensors to monitor temperature, pressure, and other parameters. If any of these sensors malfunction, it can lead to a shutdown. Common sensor issues include faulty wiring or sensor drift.
- Blocked flue: If the flue becomes blocked, the boiler will shut down to prevent the build-up of dangerous gases. A blocked flue can be caused by debris or bird nests.
- Gas supply issues: If there is a problem with the gas supply, such as a leak or low pressure, the boiler may shut down as a safety measure. Gas supply issues should be addressed by a qualified technician.
If your gas boiler shuts down, it is important to identify the cause and address it promptly. In some cases, simple troubleshooting steps can resolve the issue. However, if you are unsure or unable to fix the problem yourself, it is recommended to contact a professional heating engineer for assistance.
How to check the system
Checking the gas boiler system regularly is important to ensure its efficiency and safety. Here are some steps to follow when checking the system:
- Inspect the boiler: Start by visually inspecting the boiler for any signs of damage or wear. Look for leaks, cracks, or rust that may indicate a problem. Check the flue pipe for any blockages or obstructions.
- Check the pressure: The boiler’s pressure should be within the recommended range. Use a pressure gauge to measure the pressure and compare it to the manufacturer’s specifications.
- Inspect the radiators: Check each radiator in the system to ensure they are heating up evenly and there are no cold spots. Bleed any trapped air from the radiators if necessary.
- Check the thermostat: Make sure the thermostat is functioning properly and set at the desired temperature. Test it by adjusting the temperature and ensuring the boiler responds accordingly.
- Inspect the gas supply: Check the gas supply to the boiler to ensure there are no leaks or issues. If you smell gas or suspect a leak, turn off the gas supply immediately and contact a professional.
- Test the safety features: Test the safety features of the boiler, such as the pressure relief valve and the carbon monoxide detector, to ensure they are functioning correctly.
- Consider a professional inspection: It is recommended to have a professional inspect and service the gas boiler system annually to identify any potential issues and ensure it is running efficiently.
By regularly checking the gas boiler system, you can identify and address any issues before they become major problems. This will help to ensure the system’s performance, efficiency, and safety.
Troubleshooting
Gas boilers can experience various issues that may affect their performance. Here are some common troubleshooting steps to help you identify and resolve problems:
Problem | Possible Cause | Solution |
---|---|---|
No Heat | Thermostat not set correctly, power outage, gas supply issue | Check thermostat settings, ensure power is on, check gas supply |
Low Pressure | Water leak, faulty pressure relief valve, air in the system | Inspect the boiler for leaks, replace faulty valve, bleed air from the system |
Strange Noises | Air in the system, faulty pump or motor | Bleed air from the system, inspect and replace faulty components |
Constant Cycling | Thermostat set too high, faulty thermostat, blocked heat exchanger | Adjust thermostat settings, replace faulty thermostat, clean heat exchanger |
Ignition Failure | Gas supply issue, faulty ignition system | Check gas supply, inspect and repair ignition system |
Pilot Light Keeps Going Out | Gas supply issue, faulty thermocouple | Check gas supply, replace faulty thermocouple |
If you are unable to resolve the issue on your own, it is recommended to contact a professional heating technician for further assistance. They have the expertise and tools to diagnose and repair complex problems with gas boilers.
Q&A:
How does a gas boiler work?
A gas boiler works by burning natural gas or propane to heat water, which is then circulated through radiators or underfloor heating systems to warm up a building. The heat from the burning gas is transferred to the water through a heat exchanger, and the hot water is then pumped to the radiators or underfloor pipes.
What are the different heating cycles in a gas boiler?
A gas boiler goes through several heating cycles to maintain a comfortable temperature in a building. These cycles include the ignition cycle, where the burner ignites the gas, the heat exchanger cycle, where the heat from the burning gas is transferred to the water, and the circulation cycle, where the hot water is pumped to the radiators or underfloor pipes. The boiler also has a standby cycle, where it waits for the thermostat to signal the need for heat.
How does the pressure in a gas boiler affect its performance?
The pressure in a gas boiler is crucial for its proper functioning. If the pressure is too low, the boiler may not be able to heat the water efficiently, and there may be a lack of hot water or heat in the building. On the other hand, if the pressure is too high, it can put strain on the system and potentially cause damage. It is important to regularly check and maintain the pressure in a gas boiler to ensure optimal performance.
What are some common troubleshooting tips for gas boilers?
There are several troubleshooting tips for gas boilers. Firstly, check if the thermostat is set correctly and functioning properly. If the boiler is not producing heat, make sure the gas supply is on and there are no issues with the gas valve. Additionally, check if the pilot light is lit, as a blown-out pilot light can cause the boiler to stop working. If these steps do not solve the issue, it is recommended to contact a professional heating engineer for further assistance.
What are the different processes involved in a gas boiler?
A gas boiler involves several processes to heat water and provide heat to a building. These processes include the combustion process, where the gas is burned to produce heat, the heat transfer process, where the heat from the combustion is transferred to the water through a heat exchanger, and the circulation process, where the hot water is circulated through the radiators or underfloor pipes. These processes work together to ensure efficient heating and comfort in a building.
How does a gas boiler work?
A gas boiler works by burning natural gas or propane to heat water, which is then circulated through pipes and radiators to provide heat for a building or home.
What are the heating cycles in a gas boiler?
A gas boiler goes through several heating cycles. During the first cycle, the burner ignites to heat the water. The second cycle involves the circulation of hot water through the pipes and radiators to provide heat. The final cycle is when the burner turns off and the system cools down.